How is the Cost of UV LED Curing? A Complete Breakdown for 2025
What is UV LED Curing?
UV LED curing technology uses light-emitting diodes (LEDs) that emit ultraviolet (UV) light to instantaneously dry or cure inks, adhesives, and coatings. UV LED systems are far more efficient, durable, and environmentally friendly compared to traditional mercury lamps.
How is the Cost of UV LED Curing?
UV LED curing is changing the landscape in printing, electronics, automotive, and medical manufacturing. But, one of the most frequent and important questions asked is how is the cost of UV LED curing is determined. In this article, we provide a complete breakdown of the costs associated with UV LED curing, investigating initial investment costs, recurring operational costs, savings, and future costs in the future. As a business owner or a production manager, knowing the total cost of ownership (TCO) and return on investment (ROI) of the systems will benefit you in making the right business decisions.
Why is Cost Important in UV LED Curing?
How is the cost of UV LED curing? Cost is always a major consideration when changing technologies. Business decision-makers always want to know:
• Does it provide value?
• Are there long-term savings?
• Will the return come quickly?
In this regard, UV LED curing technology poses benefits alongside its challenges. In this case, the total cost is more than just the “sticker price”. It also incorporates “hidden costs” such as installation, energy consumption, maintenance, and life span.
Factors Influencing the Cost of UV LED Curing
Key factors that affect price are:
1. System Size
Higher curing widths (12”, 24”, etc.) require additional LEDs and increase system cost.
2. Wavelength Choice
Custom wavelengths influence pricing, though 365nm and 395nm systems are the standard.
3. Power Output
Higher-intensity systems (10W/cm² or more) boost pricing and consume more power.
4. Cooling Method
• Water-cooled systems have better performance, but a higher price.
• Air-cooled systems are more affordable.
5. Substrate and Application
Use-case scenarios like printing or adhesives, along with various substrates like glass, plastic, and metal, require application-specific, tailored systems, thus affecting pricing.
6. Compatibility with Ink and Adhesive
Costs to be incurred due to the operation are impacted by certain specialized UV inks or adhesives.
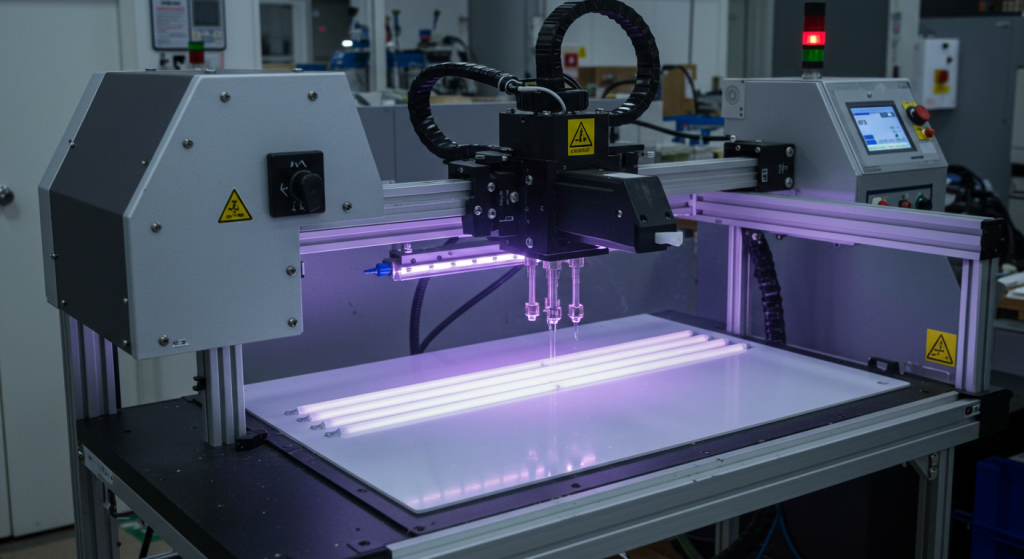
Operational and Maintenance Costs
Let’s analyze the operational expenditure of UV LED curing systems.
- Energy Efficiency
Compared to mercury lamps, UV LED systems cut electricity usage by 60-80%. This translates to over $1,000 in annual energy savings.
- UV Lamp Lifespan
- Mercury lamps: 1,000–2,000 hours.
- UV LED lamps: 10,000–20,000 hours.
Reduced lifespan costs and increased durability lead to fewer replacements and reduced costs of lamp replacement.
- Maintenance
Due to no bulbs or reflectors within UV LED systems, maintenance expenses are further reduced.
- Downtime Cost
UV LEDs incur no warm-up downtime and therefore, production downtime is minimized, enhancing productivity.
Cost Comparison: UV LED Vs. Traditional UV
Evaluating curing technologies always needs to begin with comparing UV LED to traditional Mercury-based UV lamps to capture both short-term investment and long-term returns.
- Upfront Investment
The investment in a UV LED system is higher because of advanced components and cooling technology. Conversely, traditional UV lamps have a lower purchase price but require increased maintenance costs and more frequent replacement.
- Energy Consumption
With an increased efficiency of up to 70%, UV LEDs consume less power, greatly decreasing operational costs. Power-hungry traditional UV lamps add to operational expenditures.
- Lamp Lifespan and Upkeep
UV LED modules have a lifespan of 10,000 to 20,000 hours. This is 5-10 times longer than mercury vapor lamps, which only last 1,000 to 2,000 hours. This not only means fewer replacements, but also lower maintenance, less downtime, and reduced servicing.
Environmental and Operational Costs
UVET offers a variety of extremely effective LED UV inspection light sources in addition to curing systems. These lights make it possible to conduct precise and effective inspections, enabling users to find and fix flaws, impurities, and irregularities that might affect the quality of the finished product.
- Payback Period
UV LED systems have been shown to provide ROI in 1-2 years. According to RadTech, this makes UV LEDs a financially advantageous long-term investment.
- ROI and Economic Benefits
Most businesses would benefit financially from investing in UV LED technology.
Cost Reductions
• Lower electricity costs
• Less frequent lamp replacements
• Reduced downtime
Increased Efficiency
Faster curing results in an increase in throughput. Time translates to money.
Sustainability Rebates
Due to meeting environmental regulations, UV LEDs may qualify for energy efficiency rebates.
Custom Design
Modular construction allows scaling your UV investment to business growth.
Application-Based Cost Analysis
Let’s look at the breakdown by application:
Printing
• UV LED inkjet curing: $8,000–$15,000
• Heat-sensitive substrate compatibility reduces waste costs.
Coatings & Adhesives
• Material expenses are reduced with accurate cure control.
• Bond integrity is improved with lower heat, reducing rework.
Electronics/PCB Assembly
• Accurate curing reduces defects.
• Sensitive components are protected from overheating with UV LEDs.
Is There a Return on Investment for UV LED Curing?
- For Small Businesses
Yes. Long-term value can be found with entry-level systems priced under $5000.
- For Industrial Users
Absolutely. Significant savings in energy and labor costs recuperate the higher initial investment.
- For Niche Applications
Performance efficiency is guaranteed with custom-designed systems specific to substrates and materials.
Conclusion
Ultimately, how is the cost of UV LED curing? The answer is that Energy requirements alongside application needs determine system size and cost. Overall, traditional UV systems have a lower initial investment; however, UV systems have a much lower total cost of ownership. Cost savings come from long-term reduced maintenance and replacement, faster processing, and the need for fewer replacement parts. These technologies offer businesses across printing, coatings, electronics, and adhesives new opportunities that are smart, scalable, and sustainable. Visit UVET.