What Materials Can Be Cured with UV LED?
In the multifaceted world of advanced manufacturing, 3D printing, electronics, and industrial coatings, what materials can be cured with UV LED poses a challenge. Curing technology for UV LED has become a hot topic, and for good reason: it is faster, energy-efficient, generates low heat, and provides a cleaner work environment. However, what materials can undergo this light-curing technique? In this article, we will discuss UV LED curable materials, their chemical properties, application areas, and details about expanding technology devices around the world.
Features of UV LED Curing: What is it?
UV LED curing, as the name implies, is the curing of a material using Ultraviolet (UV) light. This light is derived from light-emitting Diodes (LEDs) and causes a certain photochemical reaction. In our context, photochemical reaction is the transformation of liquid materials such as resins, adhesives, coatings, and inks into solid forms. This is achievable due to special compounds known as photoinitiators, which absorb UV light and induce polymerisation and cross-linking.
Benefits of LED Systems Over Traditional Mercury UV Lamps
Unlike traditional mercury UV lamps, UV LED systems offer the benefits of
Low Temperature Curing
- Longer years of service of about twenty thousand hours or more.
- Power consumption and emissions, in terms of environmentally friendly factors, become less.
- Use of Eco-friendly materials, aiming at minimal VOC emissions.
The Primary Materials Available for UV LED Technology
The process of UV LED curing makes industrial manufacturing easier, faster, and more efficient. Below are the categories of materials that can undergo UV LED curing.
Curable UV Resins
UV curable resins are the base of the rest of the applications of LED curing. Considered as the base for many different LED curing options, these materials undergo rapid polymerisation when exposed to UV LED light. This results in the formation of tough and long-lasting durable finishes or structures. Other common types include:
- Acrylic resins, known for their fast curing and great surface adhesion properties.
- Urethane acrylates, well known for their flexibility and low scratch ability, which makes them ideal for coatings and inks.
- Epoxy resins are high-strength and resistant to chemicals and high temperatures.
- Polyester acrylates help give a smooth finish for coating and laminating.
- Amino acrylates, which undergo a high amount of application in high-durability and high-gloss applications.
- Vinyl ester resins, guaranteed to have low corrosion resistance.
All these types of resins guarantee speciality tailored into optimal mechanical and thermal, chemical resistance for broad use industries such as automotive and electronics.
UV Curable Adhesives
Medical devices, automotive components, optics, and electronics all make extensive use of UV LED adhesives. These adhesives are useful due to rapid curing, low shrinkage, and strong bonds on difficult-to-adhere surfaces.
Examples Include:
• UV adhesives for glass and plastic bonding
• Biocompatible adhesives for medical devices
• Optical adhesives for display panels and lenses
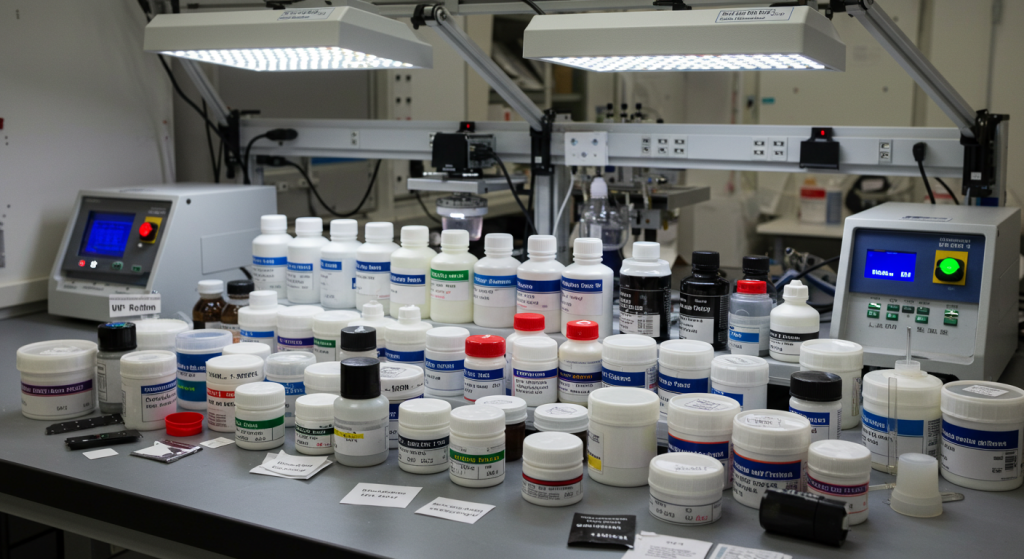
UV Curable Coating
UV coatings and acrylate coatings add beauty and increase strength by providing scratch and chemical resistance. They can be used on wood, plastic, glass, metal, and composite materials and can create high gloss and matte finishes.
Popular Applications:
• Wood and Fruit Furniture
• Automotive finishes
• Glass and electronic protective coatings
UV Curable Inks
UV inks dry instantly, provide excellent colour reproduction and vivid colours. Their uses include:
• Inkjet and flexo printing
• Labelling and packaging
• Silk and offset print
Paper, plastics, metals, and glass can be printed using these inks because they are exceptionally durable, and their print quality is unmatched.
The Tuning of Light Wavelengths and its Benefits
The UV LED systems operate at specific wavelengths targeting the absorption spectra of different photoinitiators in UV curable materials. The most common and effective wavelengths for industrial UV LED curing are the following:
• 365nm – Used very often for thicker coatings and some adhesives;
• 385nm – A universal wavelength dominating many applications;
• 395nm – The best for general-purpose curing, especially in printing;
• 405nm – Useful for some specific photoinitiators and some DLP 3D printing resins.
These wavelengths largely fall into the UVA range (315-400nm), where it is considerably less harmful than UVB (280-315) or UVC (100-280), but still have enough energy to aid in the breakdown reaction of polymerisation. A perfect match between the UV LED’s wavelength output and the photoinitiators’ absorption peak is vital for efficient and complete polymerisation and cross-linking to take place. In this manner, a dense propane structure made of a three-dimensional network of chains referred to as polymers is created, thus turning a liquid into a solid with enhanced properties.
Technical Aspects of UV LED Curing
Science behind the phenomena offers better clarity towards choosing the material.
Photoinitiators
Are those compounds that absorb ultraviolet rays and kick start the polymerisation process, specific to each material formulation, require the photoinitiators compatible with the LED wavelengths, such as 365nm, 385nm, 395nm, and 405nm.
Polymerisation and Cross-Linking
UV curing uses monomers and oligomers to make solid polymers. Cross-linking adds even more strength to the structure and improves properties such as
• Hardness
• Adhesion
• Chemical resistance
• Scratch resistance
Curing Speed and Efficiency
UV LED curing is the fastest form of curing. Many coatings and adhesives cure in under 1 second, which improves throughput and lowers labour costs.
Low Temperature Curing
UV LEDs, unlike mercury lamps, do not produce excessive heat. This enables curing on heat-sensitive substrates like plastics, electronics, and textiles.
Environmental Benefits
• Zero or Low VOC Emissions
• Energy efficient
• Longer lifespan of equipment
• Less hazardous waste
How to Select Materials Compatible with UV LED?
Here are a few recommendations:
1. Make Sure the Wavelength is Compatible: Check if the resin or adhesive is compatible with the wavelength radiated from your UV LED system.
2. About the Substrate Requirements: Think about the exposure to the environment, adhesion and flexibility.
3. Assess the Mechanical Characteristics: Find out the level to which the hardness, elasticity, or chemical resistance is desired.
4. Cure Time: Select the formulation that aligns with your quality standards and turnaround time.
The Advantages of UV LED Curing Technology
Due to the ever-growing need for energy-efficient, green and high-speed manufacturing, UV LED curing is spearheading the change. It is changing the way we coat, bond, and fabricate print.
Understanding what materials can be cured with UV LED allows manufacturers and engineers to innovate for products and hobbies.
Conclusion
The growing applications of UV LEDs span from resins to adhesives, coatings, and even inks. Whether used in 3D printing, dental resins, industrial coatings, or encapsulating electronics, UV LED curing offers unparalleled speed and precision alongside energy efficiency. The list of materials that can be cured with UV LED goes beyond chemical compatibility; it integrates a specific industry’s needs and its innovation goals. What are your thoughts?